Basic physical properties of hardchrome
HARDCHROMIUM ELECTROPLATING
Microhms per cm
HARDNESS: 65-70 Rockwell C, or 800-1250 VPN
LINEAR EXPANSION: 8.1 X 10 to the power of minus 6
MELTING POINT: 1800 Degrees
CRYSTAL FORM: Body Centre cubic
CRESISTIVITY/CO-EFFICIENT 13
ATOMIC NO.: 24
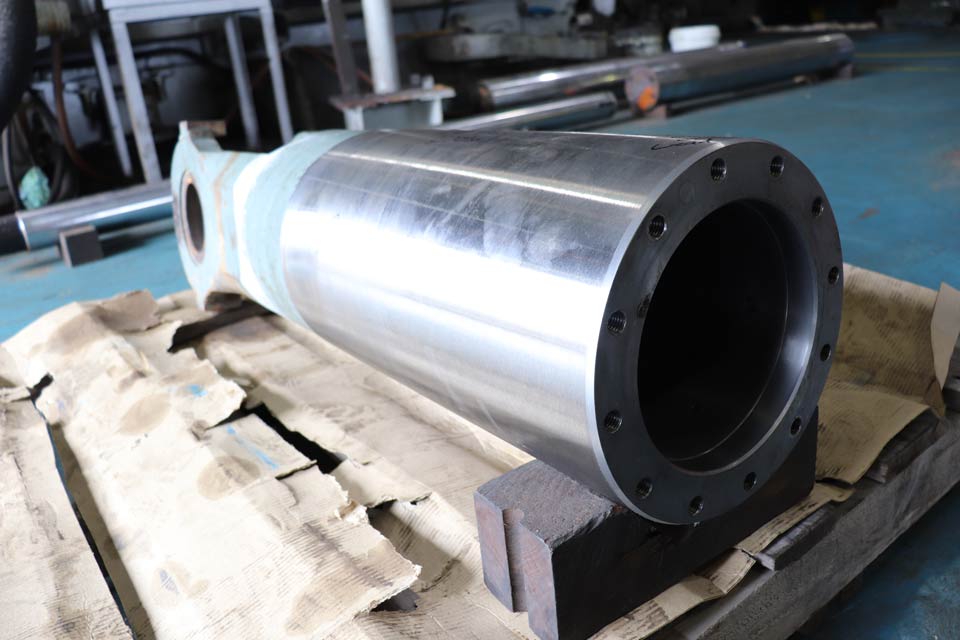
Throughout industry there is a use for hardchromium plated components. When these parts shown signs of wear and tear they should be withdrawn from service and in most cases they are reclaimable.
Coal, sand, millscale and dust particles all contribute to abrasive wear on equipment and prolonged life is achieved from the use of chrome. Rams, cylinders, spools of various types from many different industries benefit from hardchrome to overcome the problems of both wear and corrosion.
Components which, in the past, have been considered throw-away items, can be reclaimed many times over by hardchrome plating, and will operate as well as, or even better than, new ones. In the oil, mining and chemical industries, pumps and valves are particularly receptive to this type of reclamation.
Plastic, rubber and most composite materials respond to the easy release, non stick property of chrome and parts associated with movement, such as bearing journals, crankshafts, sliding components etc. They benefit greatly from co-efficient of friction, which at rest and in motion are almost identical.
The cross section of items undertaken for transport, rolling stock, shipping etc., covers diesel engine valves, cylinders, crankshafts, hydraulic rams and valve assemblies, bearing and seal areas, earth moving equipment, heavy duty trucks. The aerospace industry with components moving at high speed obtain greater durability from the application of chrome plate.
Another important aspect of hardchrome plating is that as a low temperature treatment it minimises the risk of distortion that other forms of reclamation would almost certainly induce. This is particularly advantageous for finished machined components.
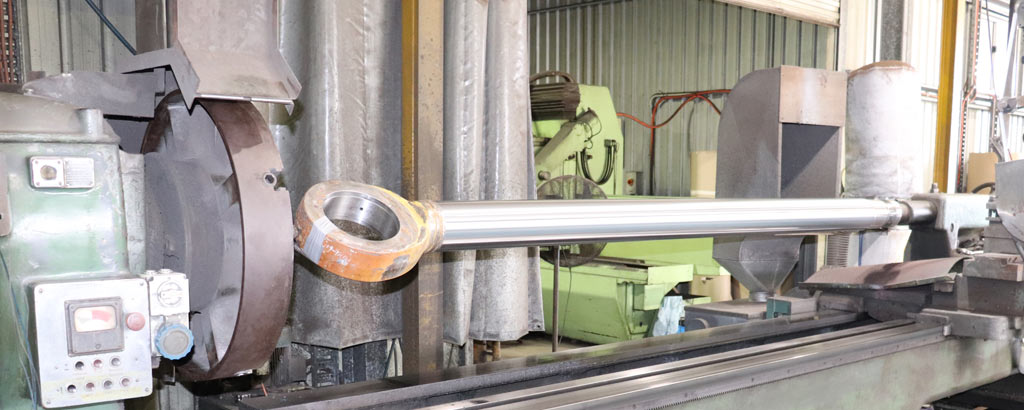
Advantages
Electroplating produces a low friction metal coating recognised for its hardness, wear resistance and anti-corrosion properties.
On examination under magnification cracks can be seen in the very fine crystalline structure, allowing for some oil retention. These can be increased under controlled conditions if appropriate. Adhesion and wear resistance remain good at high operating temperatures.
The melting point of industrial chrome is 1,800 degrees C. Of the metals in common use chrome has the lowest co-efficient of friction and other materials will adhere to it only with difficulty. When chrome has been deposited correctly for engineering purposes it is impossible to detach the deposit from the base material.
Considerations
Hardchrome plating is an excellent method of reclaiming worn, corroded or incorrectly machined parts. It should not be forgotten that chrome included as the surface finish of a component at the design stage can add greatly to the life and performance of the new part, producing substantial savings in both time and money.
The Process
Industrial Hardchrome is deposited onto a metal surface by passing a DC current through a solution of chromic acid. In special tanks the temperature is thermostatically controlled between 55 degrees and 60 degrees C. An insoluble anode ionises the solution add pure chromium is deposited on the part which acts as a cathode. This process should not be confused with the brilliant finish of bright decorative chrome, which consists of a copper-nickel deposit and a very thin layer of chrome.
Preparation and Finishing
Components which require less than 2-3 thousandths of an inch deposit are usually polished before and after processing. Preparation for heavier deposits is achieved by machine grinding. Most applications are finished to size by machine grinding, then honing and polishing to the required specification i.e N 1,2,3 finish.